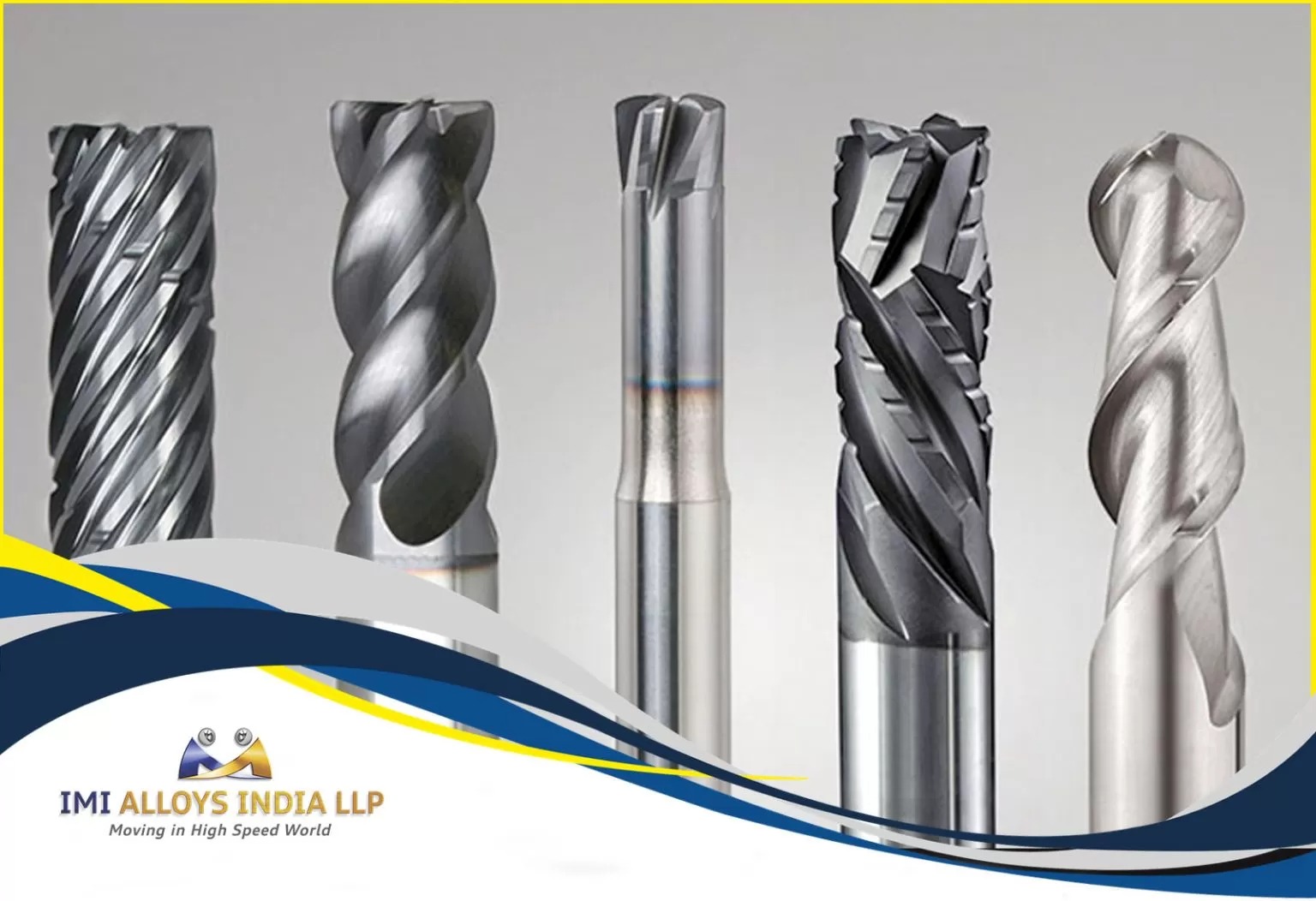
Benefits of Using Tungsten Carbide Rods in Industrial Tools
When it comes to high-performance industrial tools, one material consistently stands out: tungsten carbide rods. Known for their superior hardness, durability, and heat resistance, Carbide Rods have transformed the landscape of industrial machining and manufacturing. In this article, we’ll explore the wide-ranging benefits of using tungsten Carbide Rods, how they’re applied across industries, and why they are a must-have component in modern-day tooling.
What Are Tungsten Carbide Rods?
Tungsten carbide rods, often referred to simply as Carbide Rods, are composite materials made primarily from tungsten carbide (WC) and a metallic binder like cobalt. These rods are sintered into solid bars that are then machined or ground to specific shapes and sizes, depending on their intended application.
They are widely used in:
- Cutting tools
- Drills
- End mills
- Reamers
- Wear parts
Because of their composition and strength, Carbide Rods are able to maintain their structure even under extreme working conditions.
Exceptional Hardness and Strength
One of the most notable advantages of tungsten carbide rods is their exceptional hardness. On the Mohs scale, tungsten carbide ranks about 9, just below diamond. This makes Carbide Rods ideal for cutting and machining hard materials like stainless steel, cast iron, and even titanium.
The strength-to-weight ratio of tungsten carbide is also significantly higher than that of traditional materials like steel, which helps improve tool performance and longevity.
Long Tool Life
Thanks to their wear resistance, tools made with Carbide Rods have a much longer operational life. This means less frequent tool changes, reduced downtime, and lower tooling costs over time.
Unlike high-speed steel (HSS) tools, carbide tools remain sharper for longer, delivering clean, accurate cuts without degradation.
Resistance to Heat and Corrosion
During high-speed machining, tools often encounter significant heat. Carbide Rods have excellent thermal stability, maintaining their hardness and performance at high temperatures. This makes them ideal for applications involving heavy-duty cutting, where other materials might deform or fail.
Additionally, tungsten carbide is naturally corrosion-resistant, making it suitable for use in harsh chemical environments or humid conditions.
Precision and Surface Finish
Tools made from Carbide Rods are capable of achieving high levels of precision. The rigidity of the material minimizes vibrations during the machining process, resulting in smoother surface finishes and more accurate dimensions.
In industries like aerospace, automotive, and medical device manufacturing—where tolerances are tight and quality is crucial—this level of precision is a game-changer.
Versatility in Application
Another benefit of Carbide Rods is their versatility. They can be tailored into various shapes and sizes to suit different applications, such as:
- Micro-drills for electronics
- Large-diameter cutters for metalworking
- Special form tools for custom applications
Whether it’s milling, drilling, or boring, carbide rods deliver consistent results across all tasks.
Cost Efficiency Over Time
While the initial cost of tools made from Carbide Rods may be higher than those made from traditional materials, the long-term savings are substantial. The durability and extended tool life reduce the frequency of replacements and maintenance, leading to lower operational costs.
Moreover, fewer tool changes mean faster production cycles and less machine downtime.
Enhanced Productivity and Efficiency
Efficiency is key in any manufacturing process. Tools crafted from Carbide Rods enable higher cutting speeds and feed rates, which translates into faster machining cycles. The ability to maintain performance over long production runs ensures consistent output without interruptions.
Eco-Friendly Choice
Due to their long life and reusability, Carbide Rods contribute to sustainable manufacturing. Many carbide tools can be re-sharpened or recycled, reducing the environmental impact associated with frequent disposal and replacement of worn tools.
Competitive Edge in High-Demand Industries
Industries such as aerospace, defense, automotive, oil & gas, and medical manufacturing rely heavily on Carbide Rods. The combination of strength, heat resistance, and precision gives companies using these materials a competitive edge in delivering high-quality, reliable products.
Customization and Availability
Modern manufacturers offer Carbide Rods in a wide array of specifications—lengths, diameters, and grades—allowing users to choose the exact material that suits their needs. Some suppliers even provide custom solutions for specific applications, further enhancing performance.
Final Thoughts
In conclusion, the benefits of using tungsten carbide rods in industrial tools are hard to ignore. From extended tool life and high heat resistance to superior precision and cost efficiency, Carbide Rods offer a comprehensive solution to modern manufacturing challenges.
By incorporating tools made from these advanced materials, businesses can achieve greater output, reduced costs, and improved product quality. Whether you’re in automotive, aerospace, or general machining, investing in Carbide Rods is a smart and strategic decision for long-term growth.